In modern production processes, every precision operation requires reliable technical support. For the need for precise temperature control of the hot stamping process, the temperature control instrument relay is its core. It can not only achieve stable temperature regulation, but also significantly improve work efficiency and ensure consistent quality of finished products.
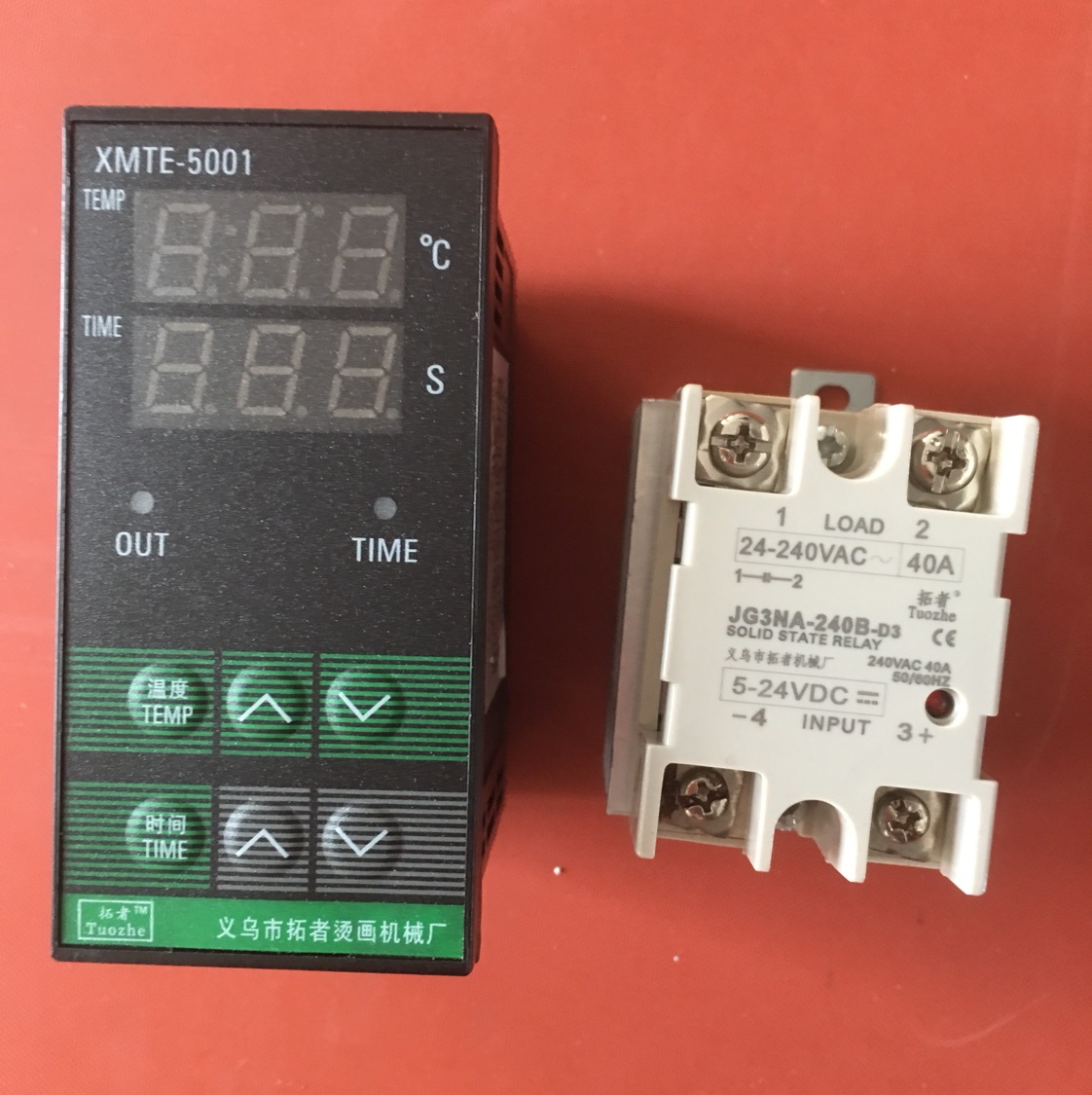
So why do more and more companies choose products sold directly by manufacturers? The answer lies in the high cost performance and rapid response capabilities brought by the transparency of the supply chain. Compared with the traditional multi-level distribution model, factory direct sales greatly reduce the cost of intermediate links, so that consumers can enjoy a more competitive price plan. In addition, direct customer communication also allows after-sales problems to be solved in a more timely and effective manner.
As one of the industry benchmarks, this top-level hot stamping machine dedicated temperature control instrument relay stands out with a number of technological innovations. First of all, it is reflected in the ultra-high sensitivity-even subtle environmental changes can be quickly captured and adjusted; followed by strong anti-interference ability, which still maintains stable operation in a complex electromagnetic environment; moreover, the humanized interface design is convenient for daily maintenance.
In addition to the theoretical superior performance, the actual test data is equally convincing. After thousands of hours of continuous operation, it was found that the average time between failures of this model was much higher than the average of similar competitors. And whether it is in extreme high temperature conditions or low temperature start-up phase has demonstrated extraordinary adaptability, for the customer business continues to escort.
The person in charge of a well-known printing factory once shared such a successful experience: "Since the introduction of this system, the overall efficiency of the production line has increased by nearly 30%, and the defective product rate has dropped by more than half. The previous phenomenon of rework due to temperature fluctuations has basically disappeared, and the saved material costs are enough to cover the input costs of new equipment." Such cases are too numerous to mention, which fully proves the importance of excellent hardware foundation for the long-term development of enterprises.
Of course, making informed decisions in the face of many brands and specifications remains a challenge. It is suggested to focus on the following aspects: first, to clarify the scope of their own needs (such as applicable models, rated power requirements, etc.), and then to evaluate the advantages and disadvantages of various indicators in combination with professional evaluation reports; Finally, don't forget to inspect the reputation of suppliers and the perfection of after-sales service system.
Looking to the future, with the continuous progress of Internet of things technology and artificial intelligence algorithms, "intelligence" will become the key word of the next wave of industrial upgrading. It is expected that the new generation of products will integrate more automated functional modules, such as remote monitoring platform access, predictive maintenance tips and other functions, further simplifying the manual intervention process while maximizing resource utilization. Grasping the frontier trend of this wave of transformation will surely create greater value space for enterprises.
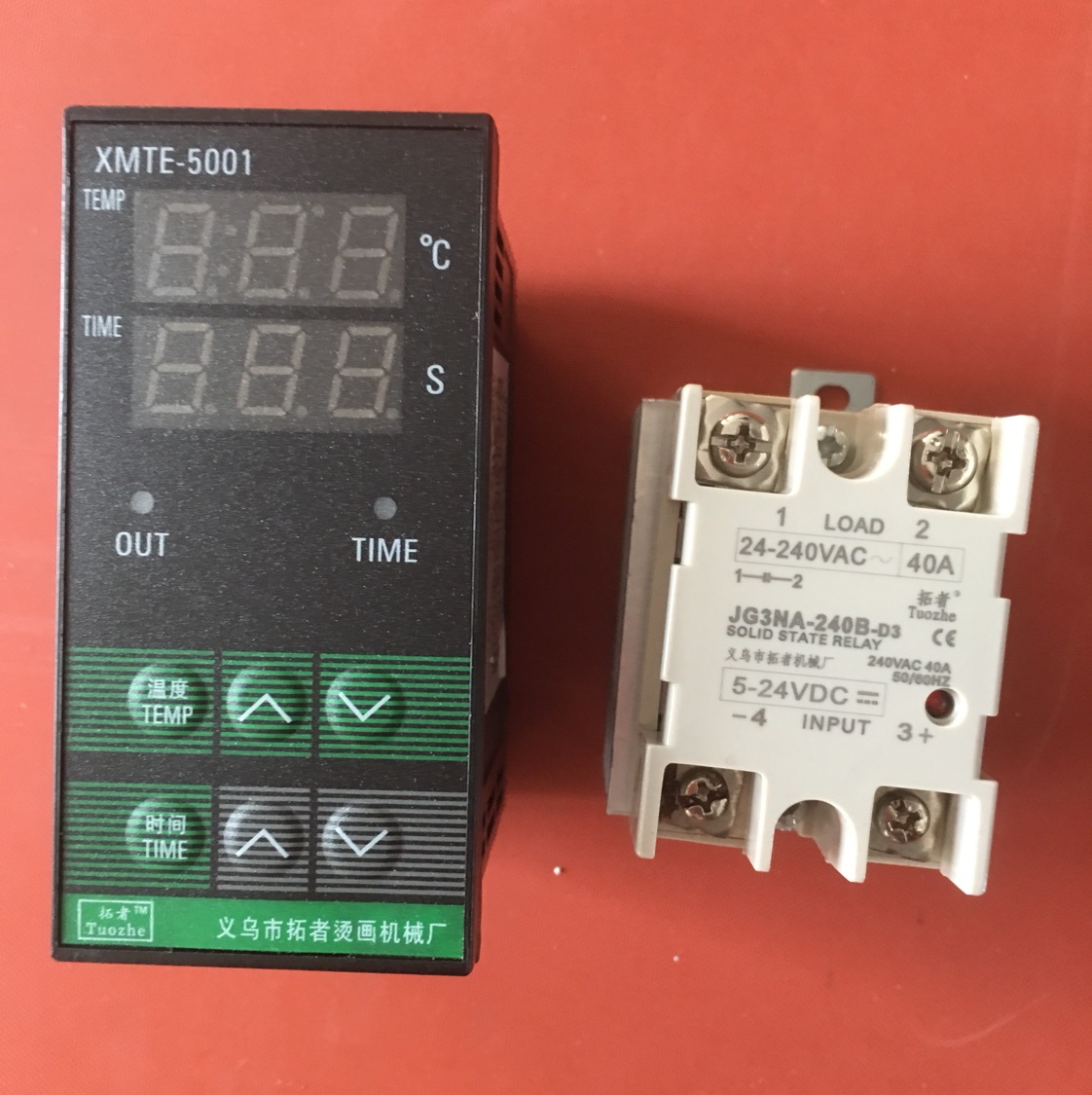