precise temperature control, efficient production-top manufacturers selling hot stamping machine special temperature control instrument relay
In modern industrial production, the stability of equipment performance is very important. Especially for hot stamping machines that require high-temperature operation, precise temperature control directly affects product quality and work efficiency. Today, we will take an in-depth look at a high-performance temperature control instrument relay directly supplied by a top manufacturer and see how it has become the first choice for many companies.
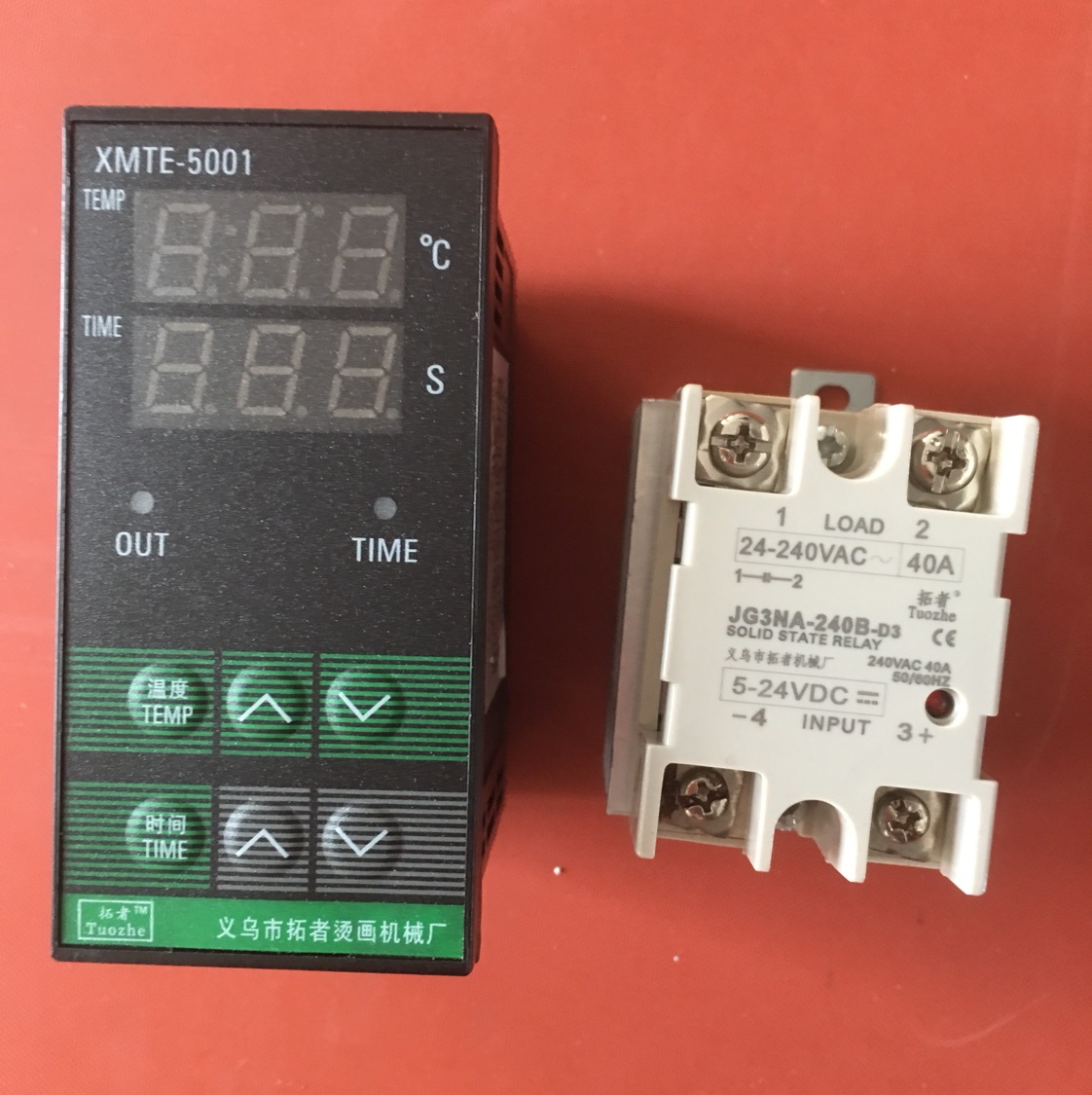
First, let's uncover the secret to the success of this top manufacturer. As one of the leading brands in the industry, they are always committed to technological innovation and quality assurance. From the selection of raw materials to the control of the production process, every link is strictly supervised to ensure that the reliability of the product can stand the test of time. This focus not only wins the trust of customers, but also sets a high standard model for the market.
So how does this temperature control instrument relay achieve precise temperature control? The answer lies in its combination of advanced sensing technology and intelligent control system. The sensor can monitor the temperature change in the current working environment in real time, and quickly feedback to the main controller; then the optimal heating scheme is calculated by precise algorithm, so as to achieve the purpose of rapid adjustment. This process is fully automated, reducing the risk of error that can be caused by human intervention.
In addition to excellent technical performance, this product also has the advantages of high efficiency and low energy consumption. On the one hand, it can significantly shorten the heating and cooling cycle, greatly improving the overall operation speed; on the other hand, due to the adoption of energy-saving design concept, it consumes less power resources while maintaining the same output level. This is undoubtedly an attractive feature for companies pursuing a green and sustainable development path.
In fact, many young entrepreneurial teams and mature manufacturing giants have chosen this series of solutions to upgrade their production line configuration. For example, after the introduction of a printing and packaging factory, the traditional manual debugging method is obviously improved, which is easy to cause overheating and damage to the finished product, and at the same time, it also reduces the operating cost by about 20%. These real-life cases are a testament to the fact that good tools can really make things simple and efficient.
Of course, how to make wise decisions when faced with the variety of brands and models on the market is also a key issue. It is recommended to clarify your specific needs, including the scope of application parameters, budget constraints and other factors, and then comprehensively consider whether the candidate meets all conditions and has a good after-sales service support system. After all, only to find the most suitable one can really help themselves to the road to success.
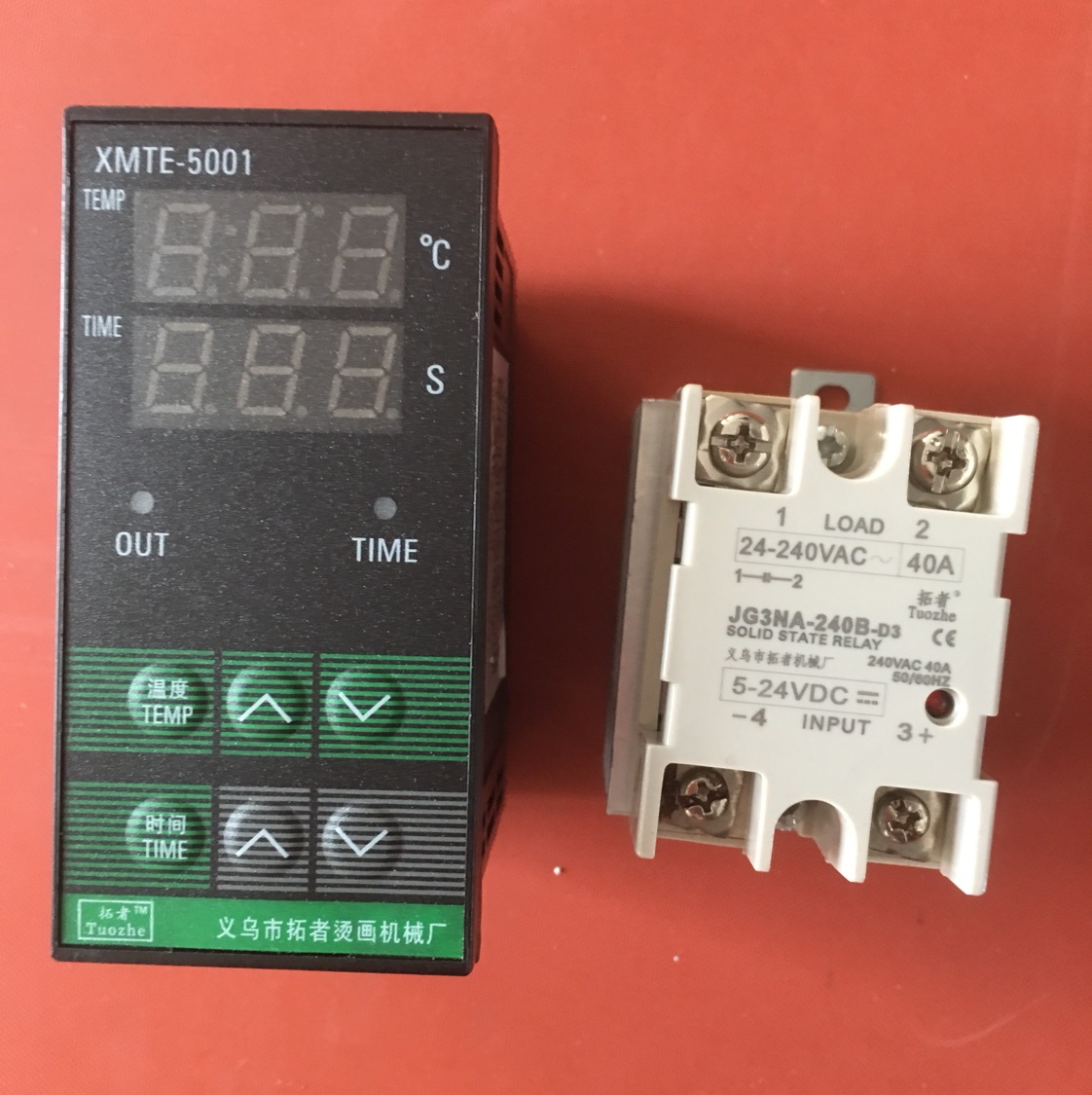