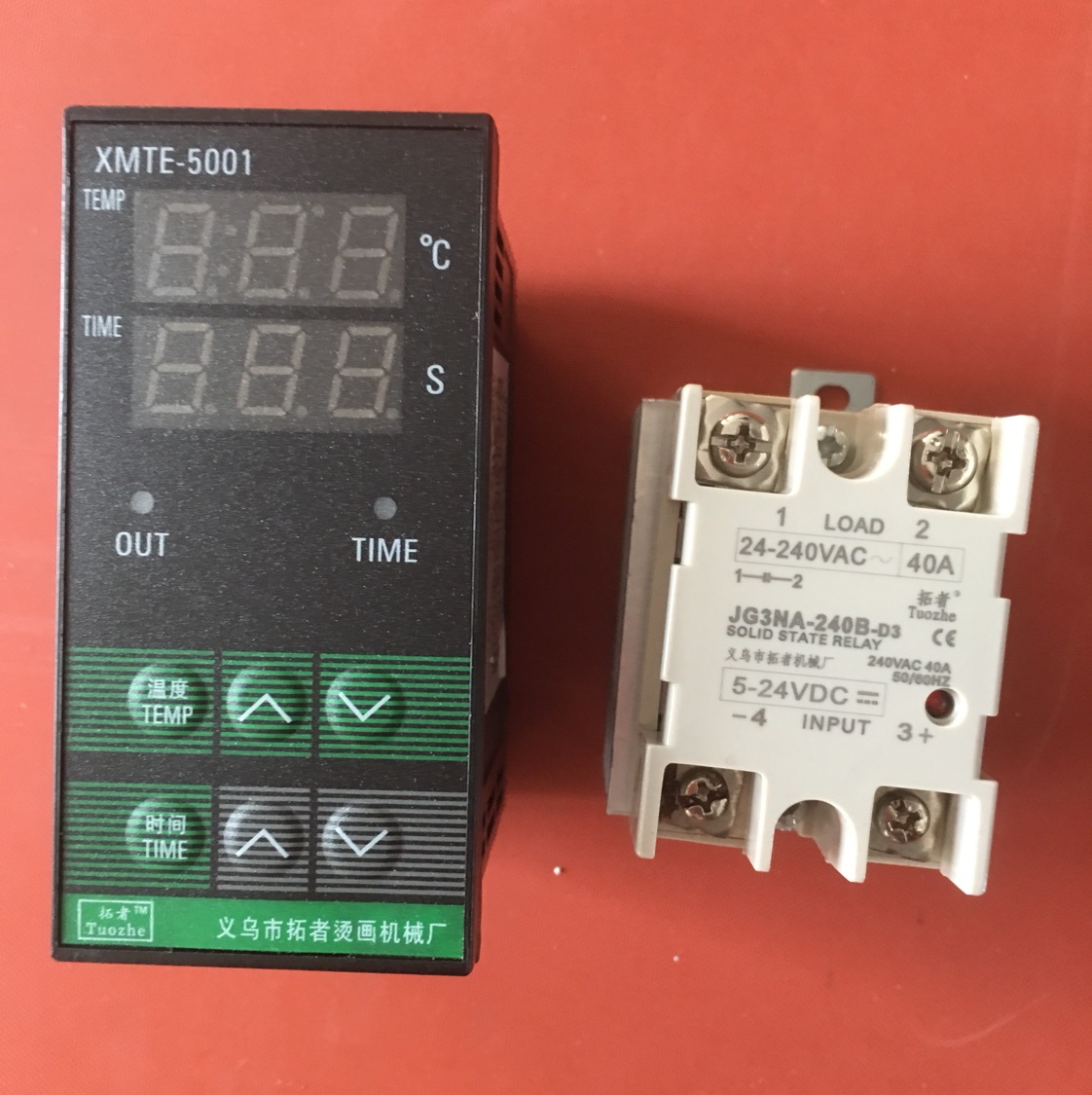
Source Factory Strives to Create Core Components of Intelligent Temperature Control for Bronzing Machinery
As a new generation of products launched by a leading domestic automation accessories manufacturer, this temperature-controlled instrument relay dedicated to industrial bronzing equipment has attracted great attention in the industry since it was launched. Relying on advanced technology platform and strict production process standards, this series of products show strong functionality and stability.
By integrating high-performance sensor computing units and multiple safety mechanisms, even in the face of complex operating environments, stable output performance can always be maintained, providing customers with a higher level of operational convenience and operational reliability.
precision temperature measurement and stable transmission control = key power source to promote the leap of production line efficiency
The device is equipped with a high-precision platinum resistance sensor and a PID closed-loop control chipset, which can complete the data sampling and dynamic correction of the surface temperature of the heating roller in a very short time, so as to ensure a constant and stable heat output effect to achieve micron-level error control level.
Its integrated solid-state relay module not only has rapid response capability, but also performs well in energy saving and consumption reduction, effectively suppressing electromagnetic interference caused by power grid fluctuations from affecting the smooth operation rhythm of adjacent electrical systems.
Multi-level security system to build a safe production defense line
In order to prevent the risks caused by emergencies to the greatest extent, this product has built-in overvoltage and overload automatic power-off protection program. Once abnormal power supply or sudden load changes are detected, the emergency fuse device will be activated immediately to cut off the main circuit connection channel, thus fundamentally curbing the possibility of accident spread.
Humanized Interface Design Shortens the Learning and Adaptation Cycle of Technician
the concise and clear large-screen display panel combined with the knob-button interaction mode enables users to easily grasp the change track of various operating parameters and make corresponding adjustment decisions in real time. The supporting detailed instructions and materials greatly reduce the entry threshold for beginners and compress the proportion of human and financial investment required for training.
strict quality inspection process forging industrial grade long-term service strength representative work
every product before leaving the factory must go through three days and three nights of uninterrupted aging test inspection checkpoints, so as to eliminate batches with hidden defects and ensure that all products delivered to users are excellent and good examples.
the box frame is made of high-strength aviation aluminum alloy and has enhanced its ability to resist external corrosion through a special anodizing process. even if it is exposed to high temperature and high humidity for a long time, it will not easily cause problems such as corrosion and peeling, resulting in structural damage and early scrapping and withdrawal from the service sequence.
Worry-free docking with mainstream models enables intelligent transformation of traditional industries
after in-depth research on the technical indicators of mainstream brands and models in the market, engineers formulated a unified assembly interface specification document, which enabled the control system to be smoothly embedded in existing production equipment to perform gradual upgrading tasks without dismantling and rebuilding the entire infrastructure network, greatly reducing the burden of upfront capital expenditure.
in addition, manufacturers have also launched personalized customization services. according to the special requirements of individual users, they have separately developed expanded communication protocol versions (such as RS485 CAN BUS, etc.) to reserve enough evolutionary space for further building the basic conditions for laying down the remote operation and maintenance management system.
terminal buyers' real comments analyze why this controller has become the first choice in the industry purchase list
summary feedback from multi-site distribution channels shows that the average unplanned downtime frequency has decreased by more than 6 percentage points year-on-year in the three months since the system went online, significantly alleviating the frequent maintenance problems caused by the aging of components, thus improving the output efficiency of the whole plant and the on-time rate of order fulfillment.
at present, a considerable number of loyal customers have started the second batch of replenishment order plans and included relevant spare parts in the scope of regular storage planning to give priority to storage in order to cope with the shock waves of various emergencies that may occur in the future, maintain the smooth flow of the supply chain, and truly be prepared to deal with challenges calmly.